“買好設(shè)備不如用好設(shè)備”
曾經(jīng)在日資企業(yè)工作的時候,接觸到設(shè)備中竟然有一臺1937年產(chǎn)的車床,設(shè)備表面干凈、整潔,完全能夠達(dá)到加工精度要求。不僅讓人感慨萬分并,對比國內(nèi)同類行業(yè)相比,對日資企業(yè)建立徹底的預(yù)防維修體制不得不佩服并發(fā)人深思。
為了適應(yīng)生產(chǎn)的發(fā)展,必定有新設(shè)備的不斷投入,于是要形成一種機(jī)制能按少維修、免維修思想設(shè)計出符合生產(chǎn)要求的設(shè)備,按性能、價格、工藝等要求對設(shè)備進(jìn)行最優(yōu)化規(guī)劃、布置,并使設(shè)備的操作和維修人員具有和新設(shè)備相適應(yīng)的能力,總之,要使新設(shè)備一投入使用就達(dá)到最佳狀態(tài),因此我們要對與質(zhì)量有關(guān)的人員、設(shè)備、材料、方法、信息等要因進(jìn)行管理、對廢品、次品和質(zhì)量缺陷的發(fā)生防范于未然,從結(jié)果管理變?yōu)橐蚬芾,使產(chǎn)品的生產(chǎn)處于良好的受控狀態(tài)。
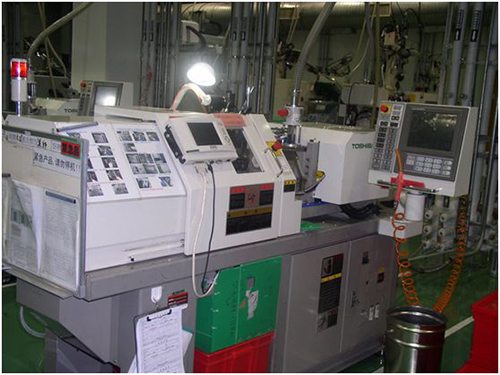
TPM是英文Total Productive Maintenance的縮略語,中文譯名叫全員生產(chǎn)維護(hù),又譯為全員生產(chǎn)保全。1950年始于美國,后流入日本,自1971年正式誕生 。TPM要求將設(shè)備的操作人員也當(dāng)作設(shè)備維修中的一項要素,這就是TPM的一種創(chuàng)新。那種"我只負(fù)責(zé)操作"的觀念在這里不再適用了。而例行的日常維修核查、少量的調(diào)整作業(yè)、潤滑以及個別部件的更換工作都成了操作人員的責(zé)任。在操作人員的協(xié)助下,專業(yè)維修人員則主要負(fù)責(zé)控制設(shè)備的過度耗損和主要停機(jī)問題。甚至是在不得不聘請外部或工廠內(nèi)部維修專家的情況下,操作人員也應(yīng)在維修過程中扮演顯著角色。
TPM發(fā)展歷程:
1. 事后修理(BM)階段?(1950年以前)
早期的維修方式,既出了故障再去維修、不壞不修。
2. 預(yù)防維修(PM)階段(1950~1960年)
PM是以檢查為基礎(chǔ)的維修,利用狀態(tài)檢測和故障診斷技術(shù)對設(shè)備進(jìn)行預(yù)測,有針對性的對故障加以排除,從而避免和減少停機(jī)
損失,分定期維修和預(yù)知維修兩種方式。
3. 生產(chǎn)維修(PM)階段(1960~1970年)
生產(chǎn)維修對部分不重要的設(shè)備仍實行事后維修(BM),避免了不必要的過剩維修。同時對重要設(shè)備通過檢查和監(jiān)測,實行預(yù)防維
修(PM)。為了恢復(fù)和提高設(shè)備性能,在修理中對設(shè)備進(jìn)行技術(shù)改造,隨時引進(jìn)新工藝、新技術(shù),這也就是改善維修(CM)。
4. 全員生產(chǎn)維修(TPM)階段(1970年至今)
生產(chǎn)操作人員參與生產(chǎn)維修,形成“全員參與”
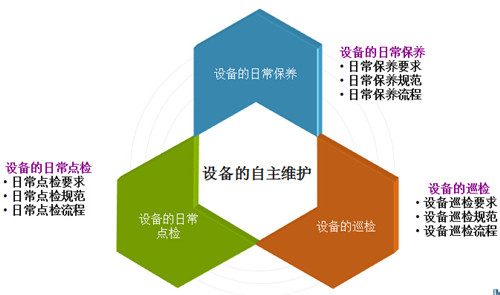
推行步驟:
1.企業(yè)最高管理層宣布推進(jìn)TPM活動,建立TPM指導(dǎo)及推進(jìn)組織。
2.設(shè)立TPM活動方針和目標(biāo),制定TPM活動計劃書
3.TPM活動培訓(xùn)和宣傳。
4.推進(jìn)5S管理。
5.設(shè)備管理規(guī)范化(各類標(biāo)準(zhǔn))。
6.開展員工提案活動、鼓勵全員持續(xù)積極的參與。
7.總結(jié)活動成果。
8.建立自主管理體制(管理程序書)
生產(chǎn)管理活動中TPM是當(dāng)今一種十分不錯的管理工具。但這并不代表企業(yè)只要實施TPM就能夠帶來多大的效果,這些還是與企業(yè)的執(zhí)行力、TPM活動的執(zhí)行方式、以及輔導(dǎo)方式有關(guān)系,通過TPM管理活動能幫助企業(yè)提升設(shè)備的綜合效率、提高企業(yè)員工的生產(chǎn)效率、提升生產(chǎn)產(chǎn)品的品質(zhì)、降低生產(chǎn)過程中的各種損耗、提升企業(yè)生產(chǎn)現(xiàn)場的整潔化與明亮化。
“沒有一項管理活動可以自發(fā)的實現(xiàn)”